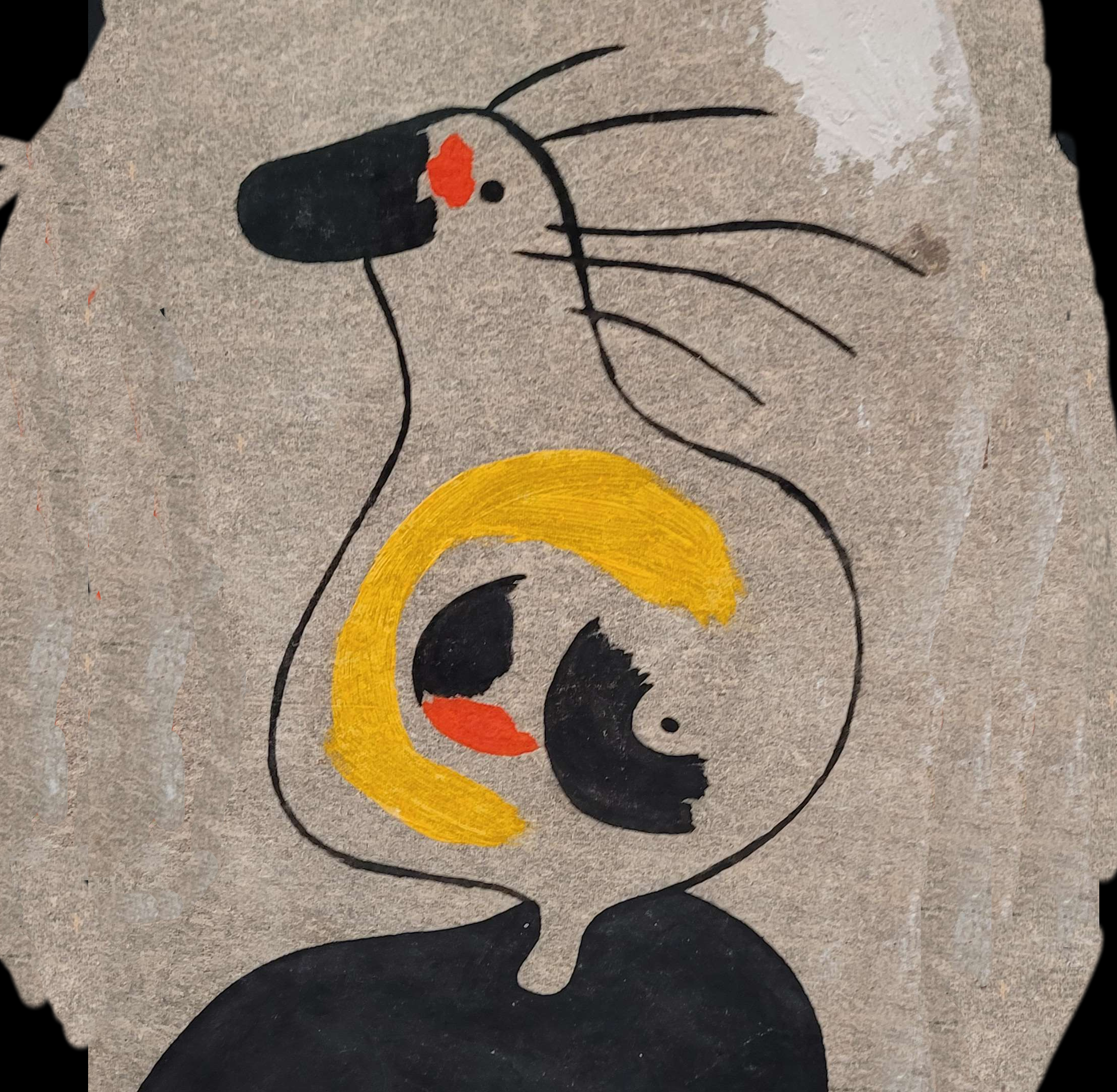

Thanks! That reminds me: one thing I did on the second and third book blocks was clamp them further in, so they were more or less flush with the boards. (I think the bookbinding book said to let it stick out a bit). That let me compress the spine an extra millimeter or two, so it wasn’t as flaired as on the first one. I think it’s always going to be a little thicker on the spine side because of all the folds and thread, but I think this looks better.
This may be a dumb question but are these wheel hubs like car hubs where you can open them up to get at the brakes? If the hubs themselves are hard to replace maybe the brake pads themselves would be easier? Something you could replace with a generic pad cut to size or something?